The ‘Other’ Reason Things are So Expensive
After years of allegedly no inflation, higher prices are making a roaring comeback.
In June, the price of used cars and trucks jumped by 45% to record highs, according to the Consumer Price Index.
Maybe you want to rent a car instead?
Well, expect to pay 87.7% more than last year.
A severe shortage of new vehicles has fueled these incredible price hikes.
Car manufacturers around the world have been pausing production.
The reason is the global lack of computer chips.
With fewer new cars rolling off the lot, demand has shifted to the used car market.
And those have gotten quite expensive as well. I recently received an insane offer from Vroom on a 2014 Honda Accord that I own:
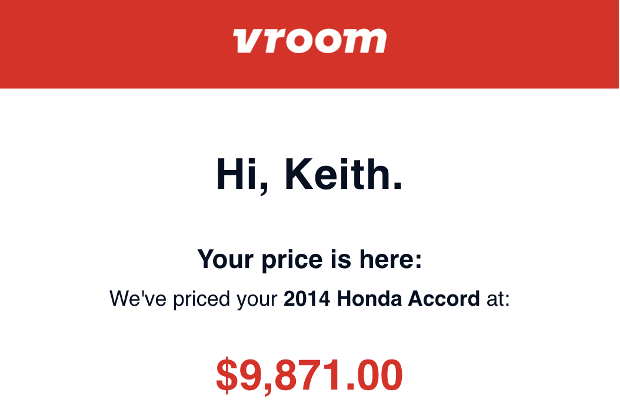
A year ago, I wouldn’t have received anything close to this.
Of course, other prices are rising, too.
Hotels and motels are almost 17% pricier than last year.
Airfares are 17.3% more expensive, which is a massive annual increase for this business.
Unfortunately, staying at home isn’t much cheaper.
TV sets and the new gaming consoles from Microsoft and Sony are hard to come by because of the chip shortage.
If you do find them in stores, expect to pay a hefty premium.
Smartphone makers are feeling the squeeze, too. The stockpiles of chips Apple and Samsung built up last year are running out. So expect more expensive iPhones soon — if you can find them, that is.
We have COVID-19 to thank for the chip shortage behind these supply gaps. Chip factories in Vietnam, China, Taiwan, and elsewhere have had to pause production.
But there’s another reason why everything is getting more expensive. A reason that affects not only electronics but also chicken, furniture, seafood, and many other products.
I’m talking about global shipping, which is in complete chaos.
Take a look at this chart from Drewry.
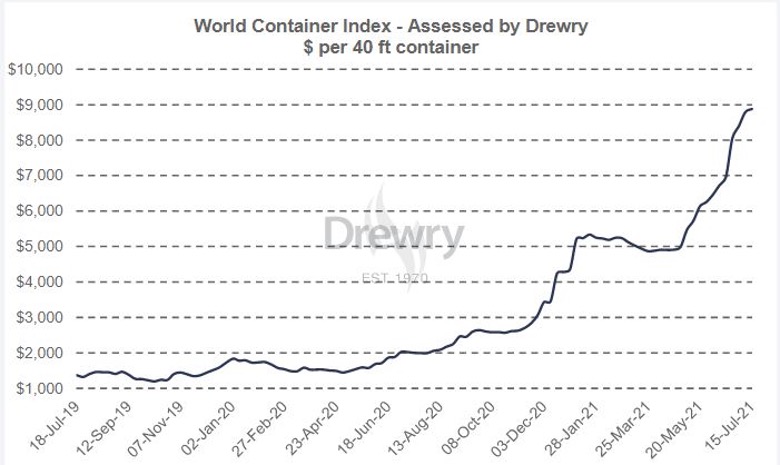
No, that’s not the price chart of a meme stock.
It’s the price of global shipping by sea.
That’s right. Companies pay up to 10 times as much for shipping as they did in 2019.
And they have to wait months and months more to get that shipping delivered, too.
This is no small matter.
The United Nations says that 80% of global trade volume is by sea.
If you count it by dollar value, that number is 70%.
Take seafood, for example. When you buy it in grocery stores here in the U.S., it may well say that it was caught in America.
But most of it is then shipped to China for processing. Then it’s shipped back to America again and ends up in your grocery store.
The same is true for many other products.
Even cars assembled in America use parts from all over the globe. Many of those parts are made here, combined with other parts abroad, and then shipped back.
Our furniture is often assembled in Vietnam, no matter where the lumber comes from. The same goes for clothing, food, and toys.
You name it, it’s been inside a container on a shipping vessel at some point before you bought it.
This worked fine for decades, until COVID-19 threw a wrench in the works.
See, before the 2010s, shipping vessels could carry at most about 6,400 containers each.
After 2010, shipping companies decided to invest in larger ships to boost profits. Today, most shipping vessels have twice the capacity, at about 11,500 containers each.
Here’s the thing: These giant ships are only profitable if they sail at full capacity.
Enter COVID-19.
Turbocharging the Shipping Industry
In March 2020, factories and ports the world over were shutting down to stop the spread of the coronavirus.
Shipping companies noticed. They worried they’d have to run their vast vessels at less than 100% capacity, which means at a loss.
So the companies canceled sailings. They ordered their ships to stay where they were. In a matter of weeks, the companies cut capacity between Asia and North America by 20%.
Given all the factories that were closing at the same time, that was a smart move.
Except that just a few months later, Americans, Europeans, and many others got bored. COVID-19 meant no restaurants, no concerts, no travel.
So people decided to splurge on things instead. And as you saw, 80% of the things we trade today travel by sea. So all of a sudden, demand for shipping skyrocketed.
America’s two largest ports broke their cargo-handling records this year.
In response to this influx of orders, factories all over the world went back online. But to produce their goods, they needed raw material shipments.
The problem is, shipping vessels had anchored where they happened to be when the coronavirus hit. But, more likely than not, that wasn’t where they needed to be now.
And remember, shipping companies can make money on their ships only when they are full.
Take Vietnam’s furniture factories, for example.
They needed lumber, which they import mainly from China and Africa.
So they asked shipping companies to go there, load up on lumber, and ship it back to Vietnam. But the shipping companies had ships all over the place that would have to sail to China and Africa.
Sailing empty-handed, with nothing to sell there, was a losing proposition for the shipping companies.
So they either waited for more orders to come in or asked for enough money to make the empty trip worthwhile.
Now expand that dynamic across the 80% of global trade that happens by sea. That’s why the price of cars, couches, chickens, and everything in between is soaring.
This also caused huge traffic jams in ports. Suddenly everyone needed ships to go from a few ports in Asia to a few ports in Europe and North America. Not to mention that COVID-19 has led to a labor shortage in these same ports.
The number of ships that had to wait more than five days in port to unload cargo soared. In the first half of last year, only 5% of ships had to wait.
By December, more than 25% of ships were stuck waiting.
And remember, every waiting ship means thousands of containers that can’t be reused.
Even once the containers are emptied, they stay here. America’s imports from China have soared 54% since last year.
But exports to China are up just 4.4%. In other words, China is running out of containers to ship our stuff in. That container imbalance will stay around until at least next year.
So it’s going to be an expensive Christmas for gift buyers.
But a great one for shipping companies.
It’s also a bonanza for factories in unexpected places. For example, Intel Corp. (INTC) announced that it’s spending $20 billion to open two new chip factories in Arizona.
Meanwhile, Taiwan’s chip giant TSMC Ltd. (TSM) pays $12 billion for its Arizona chip factory.
Those are just two examples of businesses adapting to the effect COVID-19 has had on our supply chains.
Because logistics is global, what happens in one place will affect global trade in one way or another. There’s no getting away from that, even after this pandemic.
What we can do is adapt to it. And follow the trend to make some money.